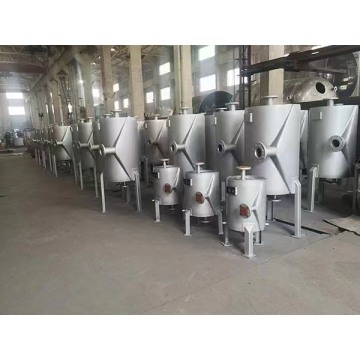
With the increase of alcohol production in recent years, the water consumption is also increasing. Every summer, the urban water shortage, insufficient water source can not guarantee normal production, and the increase of production water also increases the workload of sewage treatment. In the process of alcohol production, the
Spiral Plate Heat Exchanger not only reduces the water consumption, but also adjusts the temperature more accurately, occupies a small space, greatly reduces the failure rate, saves maintenance funds, saves energy and reduces consumption, and ensures smooth production conduct.
Alcohol production uses renewable resource grains as raw materials, which are mechanically crushed, added with water to make a slurry, and then undergo a series of processes such as liquefaction, gelatinization, saccharification, and fermentation, and then extract high-purity alcohol through distillation. During the production process, the temperature of the pre-liquefied mash during liquefaction is controlled between 80-90°C (potatoes) and 90-97°C (cereals). The preparation of liquefied mash is to quickly hydrolyze the starch in the slurry into soluble dextrin, a small amount of maltose and glucose by using a high-temperature resistant α-amylase at a certain temperature at a certain concentration of slurry. The temperature of the liquefied mash after liquefaction is relatively high, usually between 95 and 105°C, and needs to be cooled to between 58 and 62°C for saccharification. After saccharification, the saccharified mash needs to be cooled to 28-38°C before the yeast can be cultivated and fermented. Moreover, due to the growth of microorganisms in the early stage of fermentation, a certain amount of biological heat is released by biochemical reactions, and it is necessary to cool down in time to maintain a suitable fermentation temperature to ensure the smooth progress of the fermentation process. Due to the high temperature of the liquefied mash, cooling can be achieved by vacuum cooling and air cooling. The cooling method from saccharification to fermentation adopts high-efficiency heat exchanger equipment—a
Spiral plate heat exchanger.
Spiral
Plate Heat Exchanger is a kind of high-efficiency heat exchanger equipment. According to the structure, it can be divided into non-detachable (Type I) spiral plate heat exchanger and detachable (II type, III type) spiral plate heat exchanger. The spiral plate heat exchanger is made of two plates, forming two uniform spiral channels. The two heat transfer media can flow in full countercurrent, which greatly enhances the heat exchange effect. Even if the two mediums have a small temperature difference, they can To achieve the ideal heat transfer effect. The connecting pipe on the casing adopts a tangential structure, and the local resistance is small. Since the curvature of the spiral channel is uniform, the liquid flows in the equipment without a large turn, and the total resistance is small, so the design flow rate can be increased to make it have a higher performance. heat transfer capacity. The structural principle of the type II detachable spiral plate heat exchanger is basically the same as that of the non-detachable heat exchanger, but one of the channels can be disassembled for cleaning. It is especially suitable for heat exchange with viscous and precipitated liquids. A single device cannot meet the use requirements. , multiple units can be used in combination.
In alcohol production, the cooling of the mash and the cooling of the main fermentation period can be cooled by a spiral plate heat exchanger. It breaks the original traditional production mode, and also breaks the original thinking mode. The spiral plate heat exchanger has a high heat transfer coefficient, saves water resources, saves electricity resources, and reduces emissions. In addition, the spiral plate heat exchanger has a narrow and long The two uniform channels make it easier to operate to stabilize the material and perform uniform cooling.
It can also accurately control the outlet temperature. Because the main body of the equipment does not use pipes, only plates are used, the material utilization rate is high, the manufacturing cost is low, and the manufacturing is relatively simple, the quality can be guaranteed, the equipment failure is less, the maintenance is convenient, and the maintenance cost and maintenance time are reduced.